In the processing of molded pulp products such as paper egg trays, the drying process is a crucial stage that directly impacts the final quality of the products.
After pulping and molding, the paper egg trays typically contain a relatively high moisture content, ranging from 65% to 75%. Such wet trays are prone to breakage or deformation, necessitating a drying process to transform them into the final finished products. The moisture content of the dried egg trays is generally controlled within the range of 12% to 14%. Below this range, the paper egg tray’s outer edges may become wrinkled. It is also essential to avoid excessively high drying temperatures, as temperatures exceeding 40°C can cause the egg trays to become overly dry and deform.
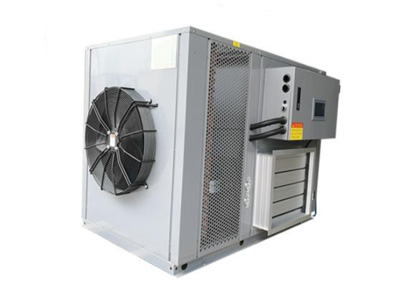
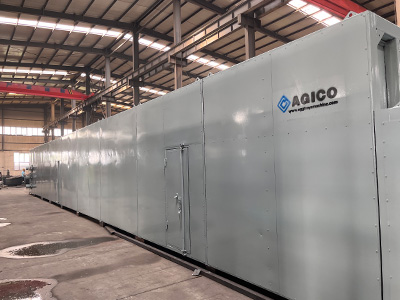
As a developer and manufacturer of paper pulp molding equipment with decades of experience, AGICO offers comprehensive drying solutions for customers engaged in paper pulp molding production. These solutions encompass drying process design, equipment layout, drying machine manufacturing, on-site installation guidance, and more. AGICO tailors the most suitable egg tray drying solutions for customers based on factors such as budget, production scale, site area, geographical conditions, climate, etc.
Contact us now for more Drying Machine details!
Drying System Working Principle
AGICO egg tray drying systems are primarily divided into two types based on the material of the drying channels: the metal steel structure drying channel and the brick-laid drying channel. The working principle of these two drying systems is essentially the same. Usually, one or multiple heating points are placed in the middle section of the drying channel to provide continuous heating. The entire drying channel is heated through the flow of hot air, achieving the purpose of egg tray drying.
AGICO Drying System Features
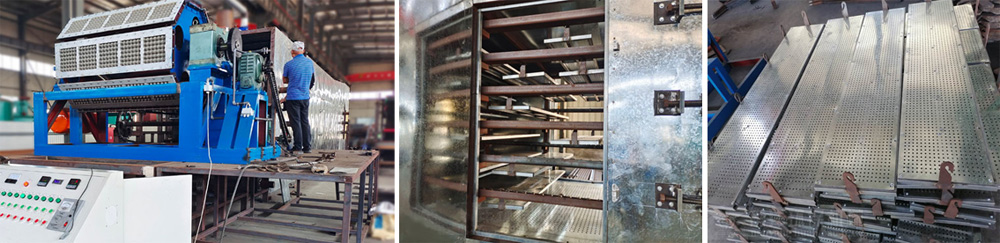
The excellent and efficient dryer and finely designed drying channel enable our egg tray drying system to have the following characteristics:
- When wet egg trays enter the drying system, both the interior and exterior are heated simultaneously, resulting in a small temperature difference. This prevents deformation and discoloration of the egg trays.
- The egg tray drying process has rapid heating and high efficiency. It allows for localized heating, minimizing energy waste and enhancing energy-saving capabilities.
- The egg tray drying machine can be directly connected and synchronized with the egg tray forming machine, increasing system stability and reducing the rate of process failures.
- The temperature in the multi-layer egg tray drying system can be controlled in segments to meet specific product requirements, providing flexibility and adaptability in the drying process.
- The egg tray drying line is equipped with a forced air supply system, ensuring more uniform and controllable drying temperatures and air distribution.
- The drying system requires a short pre-settling time, resulting in less working hours and reduced pollution.
- The adoption of an infinitely variable temperature control system makes the egg tray drying process more intelligent and automated.
AGICO Drying System Specifications
Drying System | Length (m) | Output (p/h) |
Natural drying | Customizable | 1000-2500 |
Brick kiln drying system | 40-45 | 1000-2000 |
50-55 | 2000-4000 | |
60-65 | 4000-7000 | |
Multilayer metal drying system | 25 | 1000-7000 |
Single-layer metal drying system | 40-45 | 1000-2000 |
50-55 | 2000-4000 | |
60-65 | 4000-7000 |
Quote now to get complete egg tray drying solutions!
How to Choose the Appropriate Drying Method
Brick-laid drying channels and metal steel structure drying channels are currently two mainstream methods for drying paper egg trays. In addition, some manufacturers employ natural air-drying methods to remove moisture from wet egg trays. To select the most suitable drying method, it is crucial to understand the advantages and disadvantages of each approach.
Brick-Laid Drying Line:
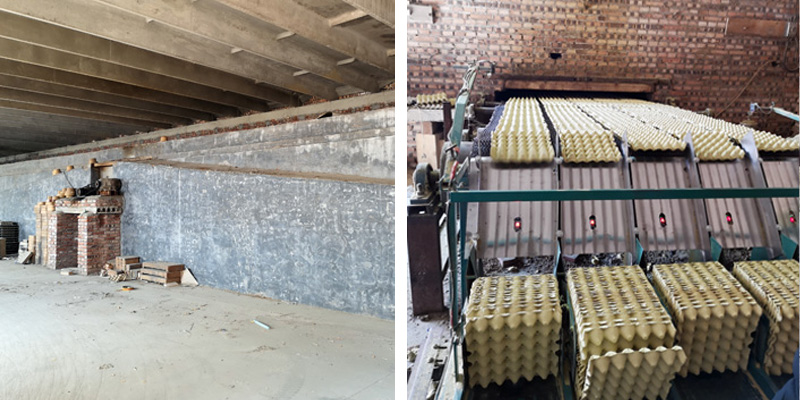
The brick-laid drying line is primarily constructed using refractory bricks and offers several notable features, including low investment cost, high thermal efficiency, long service life, ease of maintenance, and safety in operation. Depending on the local fuel availability, various fuel options can be employed, such as steam, thermal oil, natural gas, coal gas, smokeless coal, low-smoke firewood, wood chips, bark, and bamboo offcuts. In terms of heat consumption, the brick-laid concrete drying line exhibits higher heating efficiency compared to the metal steel structure drying line, as metals have significantly better thermal conductivity than stone or soil, resulting in more heat dissipation during the drying process.
Metal Steel Structure Drying Line:
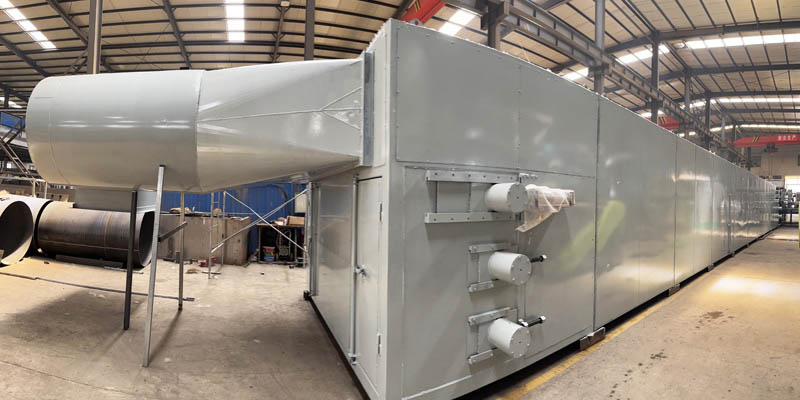
Metal steel structure drying lines primarily employ refractory steel as the main material and utilize fuel (gas), electricity, or steam (thermal oil) as the heat source. They heat the air and dry the molded paper pulp products in the hot air. The drying process involves using fans to draw out the evaporated moisture from the products, achieving rapid drying effects.
Metal drying lines can be further categorized into single-layer drying lines and multi-layer drying lines. Single-layer drying lines require larger floor space, and the workshop length should not be less than 70 meters. On the other hand, multi-layer drying lines occupy a smaller area, requiring a workshop length of at least 40 meters and a workshop height of 4.5 meters. Due to their smaller volume, multi-layer drying lines can effectively conserve heat within the drying line.
Compared to multi-layer steel structure drying lines, single-layer steel structure drying lines have a larger footprint and slightly lower costs. Customers can choose between them based on their factory size, energy availability, and specific requirements.
Natural Drying:
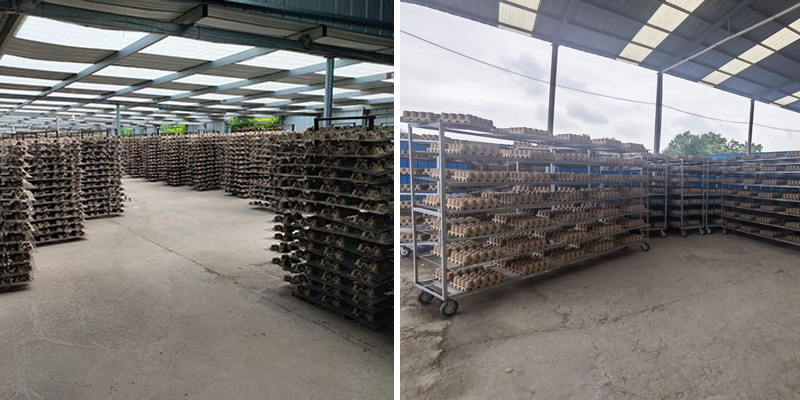
Natural drying involves placing the wet egg trays directly on racks and allowing them to dry under sunlight. This method can improve cost-effectiveness as it requires minimal expenses. Except for labor costs, it doesn’t need any drying equipment. However, it does not enhance production efficiency as drying is greatly affected by natural environmental conditions. If the egg trays encounter rainy weather, they may not dry properly, and there is a risk of mold formation. Additionally, natural air drying cannot precisely control temperature and humidity. Excessive exposure to the sun can also lead to significant deformities in the egg trays.
Conclusion:
AGICO always recommends the most suitable drying method based on the customer’s conditions and production requirements.
For customers with small production scales, limited budgets, and located in dry climate areas, the natural air-drying method can be a cost-saving option. However, for customers with larger production scales or in climates where natural air drying is not feasible, brick-laid drying lines are a preferable choice. They offer high drying efficiency and low fuel consumption. For customers who value maintaining a neat and aesthetically pleasing factory with limited space, single-layer or multi-layer steel structure drying lines are suitable options. They not only have a more appealing appearance but also feature higher automation levels, making them ideal for large-scale egg tray production.
Project Cases
In the past decade, AGICO has successfully built egg tray production lines and drying systems for over 50 customers around the globe. The company always prioritizes the interests of our customers and strives to provide them with the highest quality products and most thoughtful services. Please feel free to contact us if you are looking for drying solutions for your pulp molding business!
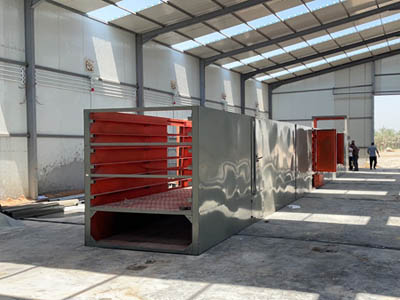
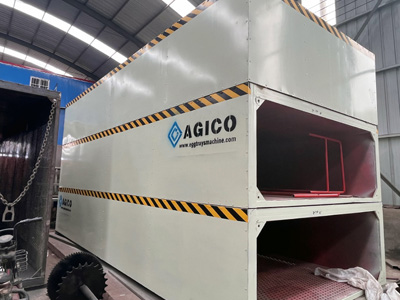