Molded pulp products are various environmentally friendly packaging products that are made from waste newspapers, recycled cardboard boxes, various biomass waste materials, etc., and are mixed into a certain proportion of pulp through processes such as pulping and blending. The pulp is vacuum adsorbed into wet pulp semi-finished products on special molds, and then dried, hot pressed and shaped to form various packaging products. The core equipment used in its production process is the pulp molding machine.
AGICO is a professional manufacturer of pulp molding equipment, capable of producing various models of high-quality pulp molding machines with a production range of 1,000-8,000 pcs/h. Adopting the principle of vacuum adsorption molding and pulp molding dry pressing technology, it can be combined with a full metal frame drying line, brick kiln drying or natural drying equipment to achieve the complete production process of molde pulp goods. Our paper pulp molding machine has a simple process, easy maintenance, automated operation, and low operating costs, especially suitable for the commercial production of low-end pulp packaging products such as pulp egg trays, cup trays, and seedling trays.
Product Features:
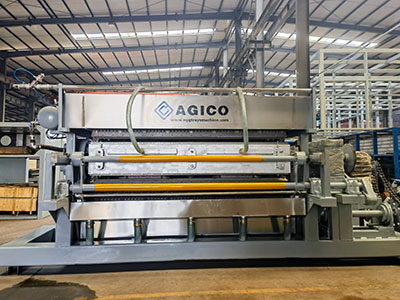
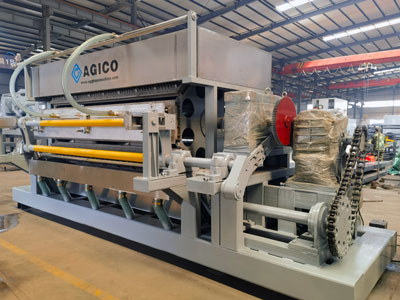
High-Quality Components
The internal bearings, bolts, and other parts of the machine are sourced from internationally renowned brands, ensuring superior quality. The entire machine is meticulously designed and undergoes multiple quality control procedures before delivery, resulting in low failure rates and safe, reliable production for users.
Efficient Drum-Type Design
Featuring a drum-type design, the machine offers high production capacity and efficiency, enabling continuous automated production. Various drum models are available, and customized designs can be provided to meet specific production requirements.
Versatile and Cost-Effective
The machine’s simple structure and low investment cost make it highly adaptable to different production needs. By simply changing the molds, it can produce a variety of pulp products, such as egg trays, fruit trays, seedling trays, cup carriers, and industrial packaging inserts.
Comprehensive After-Sales Service
AGICO provides complete after-sales support for every pulp molding machine purchased. Each machine comes with a one-year warranty, during which any non-human-induced malfunctions will be repaired free of charge. Additionally, we offer online or on-site installation guidance and commissioning services to help you begin production with ease.
Need a quotation? Contact us now!
Vacuum Forming Method
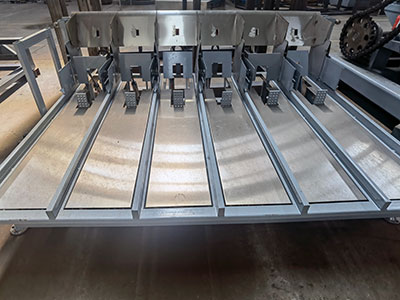
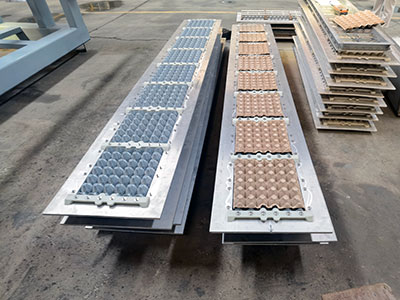
The basic principle of vacuum forming involves drawing a vacuum within the cavity of a mesh-lined lower mold submerged in pulp. Under negative pressure for a set duration, plant fibers in the pulp adhere to the outer surface of the lower mold, while water is extracted, forming the product. The forming mold features a porous structure with a mesh screen of specific aperture affixed to its surface. By applying vacuum suction, the cavity within the forming mold is evacuated, allowing fibers to deposit on the mesh surface while excess water is removed during the vacuum process.
Working Procedure:
- The male mold moves downward into the pulp pool.
- Vacuum suction draws pulp onto the mold.
- The male mold moves upward.
- The male and female molds close to apply pressure and dewater.
- The female mold transfers the blank upward and releases it with air blow.
- The product is demolded.
Forming Principle:
Pulp is stored in the pulp pool, and the mesh mold is fixed onto the female mold. The flow of pulp in the pool, combined with the vertical movement of the female mold, ensures uniform mixing. When the female mold submerges below the pulp surface, vacuum suction causes pulp fibers to deposit on the mesh mold. The mold is then lifted out of the pool and pressed against the male mold to dewater, producing a blank with higher dryness. The thickness of the molded product can be controlled by adjusting the suction time during the forming process. Since vacuum suction applies uniform pressure in all directions, the pulp-molded products achieve consistent and even thickness.
Contact us now for more machine details!
Pulp Molding Dry Pressing Technology
Modern pulp molding processes can be divided into dry pressing process and wet pressing process, both of which can use vacuum forming technology. Wet pressing technology is a process in which the forming machine directly heats the pulp body during the pulp forming process, and then performs hot pressing and trimming on the product. The forming machine of the dry pressing process does not heat the pulp blank, but has a drying process after forming. Dry pressing is the process of placing the formed product in a dryer and drying it with hot air. The dryer has a conveying device inside. In the first half of the dryer, the temperature is generally adjusted between 200 ℃ and 300 ℃, and in the second half, the temperature drops to between 100 ℃ and 200 ℃. The product passes through different temperature zones in the dryer and is finally dried to a moisture content range of 10% to 13%.
Compared to the wet-pressing process, the dry-pressing process produces pulp molded products with rougher surfaces. However, it requires simpler and less expensive equipment, resulting in lower production costs. This makes it a more cost-effective option for manufacturing products like egg trays, cup carriers, and seedling trays, where appearance is not a critical factor.
Product Specifications
Model | Rotary Drum | Forming Mould | Transferring Mould | Capacity (p/h) | Power (kW) |
DT 3×4 | 4-side | 12 | 3 | 1800~2300 | 3 |
DT 4×4 | 4-side | 16 | 4 | 2200~2500 | 3 |
DT 3×8 | 8-side | 24 | 3 | 3000~4000 | 3 |
DT 4×8 | 8-side | 32 | 4 | 3500~4500 | 3 |
DT 5×8 | 8-side | 40 | 5 | 4000~5000 | 4 |
DT 6×8 | 8-side | 48 | 6 | 6000~7000 | 4 |
DT 5×12 | 12-side | 60 | 5 | 5000~6000 | 4 |
DT 6×12 | 12-side | 72 | 6 | 7000~8000 | 4 |