Pulp molding products are made using pulp as the primary raw material. They are formed on specialized molds and finalized through processes such as hot pressing or drying. These products are fully biodegradable in natural environments. Pulp molding products offer numerous advantages, including moisture resistance, mold resistance, anti-static properties, water resistance, oil resistance, heat tolerance, non-toxicity, odorlessness, and excellent cushioning performance. The raw materials consist of abundant and renewable plant fibers. These products are widely used in the packaging of industrial and agricultural products as well as food containers.
When evaluated comprehensively in terms of raw material availability, process maturity, environmental impact during production, product performance, market acceptance, production costs, biodegradability, and recyclability, pulp molding products are considered an ideal alternative to EPS (expanded polystyrene) packaging materials.
Currently, the mainstream pulp molding processes can be divided into two categories: dry pressing and wet pressing. What are the differences between these two processes? What are their respective advantages? And what types of pulp molding products are they used to produce? This article aims to answer these questions.
Pulp Molding Dry Pressing Process
The dry pressing process involves injecting pulp slurry into forming molds of the pulp molding machine through pipelines after the pulp is prepared. Excess water is removed via vacuum suction to form a wet blank, which is then air-dried naturally or passed through specialized drying channels to reduce its moisture content to around 40%. The dried blank is then shaped using a pressing mold. This process is primarily used to produce low-grade pulp egg trays and industrial pulp packaging products.
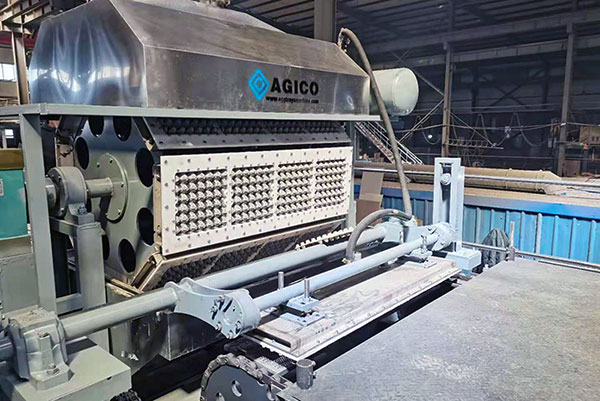
Advantages:
- Lower thermal energy consumption, reducing overall energy usage.
- Primarily utilizes pulp-based materials, allowing for the recycling of waste paper, which reduces costs and makes products more affordable.
- Produces thicker products with excellent shock absorption and compression resistance.
- Provides anti-static properties, making it suitable for packaging electronic products.
Disadvantages:
- Dry-pressed products (including semi-dry) have rough surfaces and lack aesthetic appeal.
- The thicker walls result in larger product volumes, which can be less space-efficient.
Applications of the Dry Pressing Process
Standard Industrial Packaging
This category includes low-end electronic product liners, egg trays, and fruit trays made from pulp. These products typically have a rough surface and are primarily designed for shock absorption and compression resistance, with minimal emphasis on aesthetics.
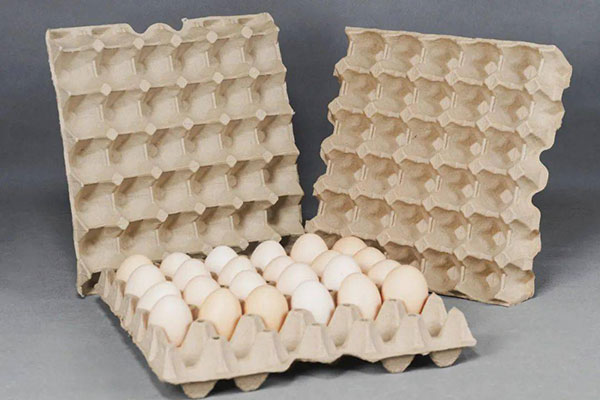
Agricultural Packaging
This includes products such as paper flower pots and seedling trays. These items are mostly produced using the dry pressing process with unbleached pulp or recycled newspaper pulp. They have lower hygiene requirements and minimal stiffness demands but require good water resistance.
Medical Packaging
In the medical field, the dry pressing process is used to manufacture disposable items such as bedpans and urinals. These products have relatively low requirements for surface aesthetics and hygiene conditions.
Pulp Molding Wet Pressing Process
The wet pressing process involves injecting pulp slurry into forming molds through pipelines after the pulp is prepared. Excess water is removed via vacuum suction, forming a wet blank, which is then immediately transferred to a hot-pressing mold for rapid compression and drying.
Advantages:
- The wet pressing process offers high production efficiency for eco-friendly tableware, as the formed product is promptly transferred for shaping, enabling fast production speeds.
- Wet blanks in this process have a moisture content of approximately 65-75%, requiring longer vacuum suction times due to the high water content.
- Products made with the wet pressing process feature a smooth, delicate surface and an appealing appearance.
- Disposable tableware produced through wet pressing has thinner walls, higher density, and reduced volume, making it more space-efficient.
Disadvantages:
- For disposable tableware with smaller draft angles, demolding can be challenging.
- Products with small radii (R corners) or shallow draft angles are more prone to mesh-breaking issues.
- The process has higher thermal energy consumption.
Applications of the Wet Pressing Process
Premium Industrial Packaging
Also known as high-end molded pulp packaging, these products are formed through wet pressing to achieve a smooth and aesthetically pleasing surface. They are commonly used for high-end electronic inner boxes, luxury razor packaging, premium clothing boxes, and eyeglass cases. These products require exceptional precision, an attractive appearance, and a higher added value compared to standard wet-pressed items.
To enhance aesthetics and increase the perceived value of the packaged products, color printing can be applied to showcase a more striking packaging effect.
Food Packaging Containers
This category includes disposable biodegradable tableware such as plates, bowls, boxes, and cake trays. These items are typically made from plant fibers such as wheat straw and sugarcane, incorporating food-grade water- and oil-resistant agents.
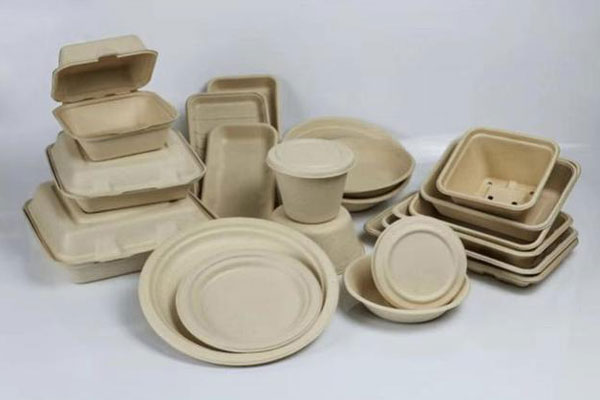
Widely used in everyday dining, dine-in settings, and food delivery, these products must meet food-grade requirements for microorganisms and heavy metals. They are produced in dust-free workshops to ensure a clean and attractive appearance.
Medical Trays
Primarily produced using the wet pressing process, these trays are designed for the storage of syringes, medications, and other medical equipment. Manufacturing takes place in dust-free workshops with strict control over microbiological standards to meet medical-grade requirements. The products are vacuum-sealed in a sterile environment.
Recreational Toys
This category includes items such as masks and coloring toys, which can be produced using both semi-dry and wet pressing processes. The surface must be smooth to retain applied dyes effectively, offering a finer, more refined tactile experience.
About AGICO
AGICO is a professional pulp molding equipment manufacturer based in China. We mainly provide dry pressing solutions for the production of paper egg trays, fruit trays, seedling trays, and other molded pulp products. Feel free to drop us a letter if you are interested in starting your pulp molding business!