Pulp molded products are environmentally-friendly products widely used in various fields such as food packaging, electrical appliance packaging, seedling cultivation, medical utensils, handicraft substrates, and fragile item cushioning packaging. These products are made using plant fiber pulp (such as wood, bamboo, bagasse, etc.) or recycled paper pulp as raw materials, which are completely recyclable.
In recent years, with governments around the world imposing restrictions on plastic packaging and consumers’ increasing awareness of environmental protection, there has been a continuous growth in the demand for green and eco-friendly packaging. As a result, pulp molded products, a new alternative, have quietly gained popularity. Furthermore, with the continuous advancement of intelligent equipment technology, pulp molding processes have made remarkable progress, leading to the emergence of numerous application scenarios and triggering a boom in the pulp and plastic manufacturing industry.
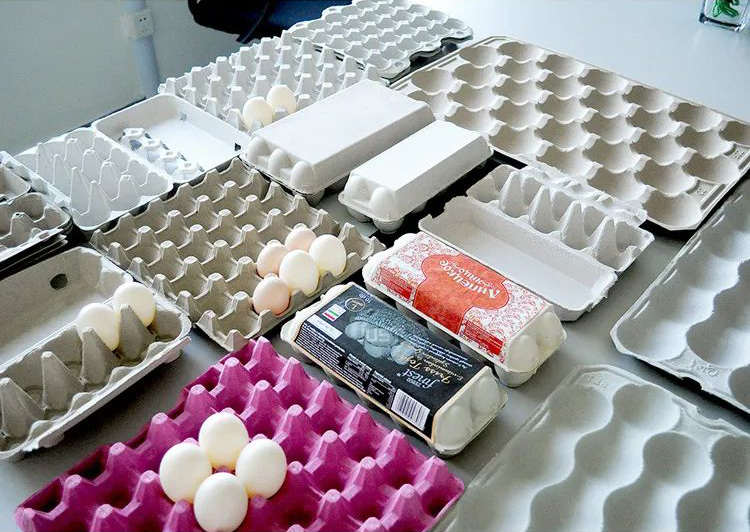
This article will provide a detailed introduction to the classification of pulp molding molds and the key points to consider in their design.
Characteristics of Pulp Molding Molds
The design of molds for pulp molding should meet the structural requirements of the target pulp molded products. When designing the structure of pulp molded products, it is essential to consider not only the usage and forming process conditions but also the requirements for mold design and manufacturing.
Therefore, before designing pulp molding molds, design firms need to conduct thorough research and analysis of the structure of pulp molded products. This is done to ensure the economic and technical feasibility and harmony between product design and mold design.
During the forming process of pulp molded products, they need to enter the mold multiple times before the final manufacturing is completed. This is because pulp molded products are formed on a single convex or concave mold and, after forming, they must be transferred in the mold cavity after the convex and concave molds are closed. The wet pulp is then transferred to the shaping mold, where it is pressurized and heated to become the finished product.
Therefore, pulp molding molds are divided into forming molds, shaping molds, trimming molds, and die-cutting molds, among others. There are two types of forming processes: adsorption forming and pressing forming. Pressing forming molds are somewhat similar to molds used for manufacturing rubber and plastic products, while adsorption forming molds are more specialized and complex.
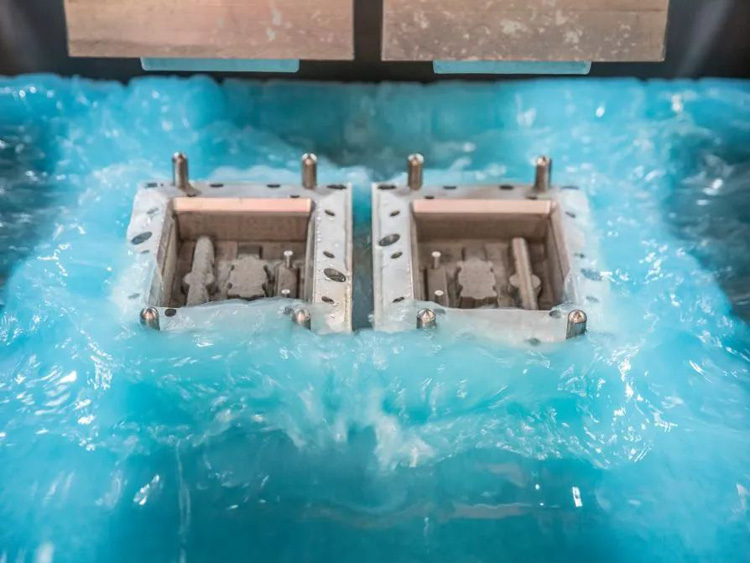
Moreover, the forming of pulp molded products is quite different from rubber and plastic products formed within the mold cavity. The pulp material used in the forming process is a water solution containing only about 10% fiber, and during the forming process, most of the water must be removed. Therefore, pulp molding molds must be mesh molds.
Key Points for Pulp Molding Mold Design
Adsorption Forming Molds
Adsorption forming molds consist of a convex mold, a concave mold, a mesh mold, a mold base, a mold cavity, and an air chamber, among others. The mesh mold is the main component of the mold. Since the mesh mold is woven from wires (metal or plastic) with a diameter of 0.15mm, it cannot form independently and must be attached to the mold surface to function.
The mold cavity is an empty space formed by the mold base and the backside of the mold, which maintains a certain thickness and perfectly matches the shape of the working surface. The convex and concave molds form a shell structure with a specific wall thickness. Small holes are uniformly distributed to connect the working surface and the mold cavity.
The mold is mounted on the template of the pulp molding machine through the mold base, while the other side of the template is equipped with an air chamber that communicates with the mold cavity.
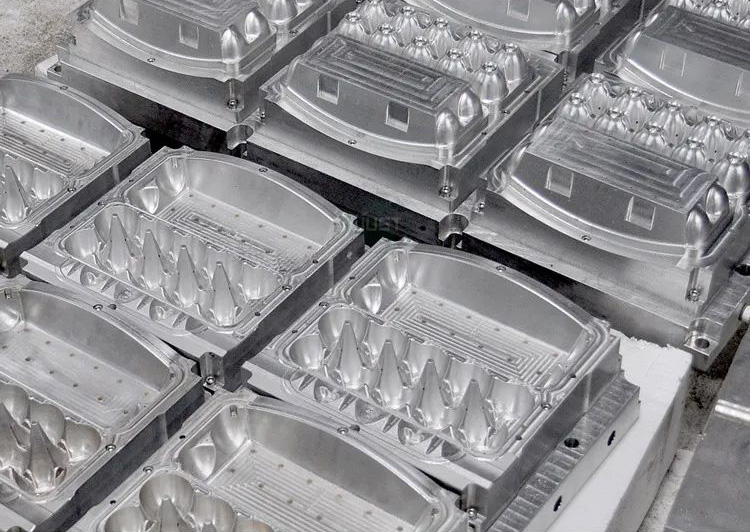
Determining the allowance in the design of adsorption forming molds is crucial. Due to water evaporation, there will be shrinkage when wet pulp is made into finished products. Different positions of the same product have irregular and varying shrinkage rates, leading to multidirectional and unpredictable changes during the forming process. This poses challenges in determining the allowance for mold design. Currently, the packaging industry does not require high precision in the manufacturing of pulp molded products, so designers mainly rely on experience to determine the allowance.
Pulp Molding Shaping Molds
Shaping molds for pulp molding are designed to provide heating, pressurization, and dehydration functions, allowing the wet pulp to undergo direct drying and shaping inside the mold. Products manufactured with shaping molds have smooth surfaces, accurate dimensions, solid texture, and good rigidity. Disposable tableware often utilizes this type of mold. In the industrial packaging field, shaping molded paper products are also used for packaging small and delicate items.
The structure of shaping molds includes convex molds, concave molds, mesh molds, and heating elements. The convex or concave molds with mesh molds have drainage and vent holes. During the production of pulp molded products, the wet pulp undergoes extrusion and then heating inside the shaping mold, which vaporizes and removes the water content, resulting in the formation of the product.
The presence of a mesh mold in the shaping mold can cause a mesh pattern on the surface of the product, and the mesh mold can quickly become damaged due to frequent extrusion. To address this issue, some mold designers have developed a meshless mold using copper-based spherical powder metallurgy. Over the past years, through multiple structural improvements and the selection of appropriate powder particle sizes, the meshless shaping molds have been manufactured with a lifespan ten times longer than that of mesh molds and at a 50% lower cost. The resulting paper products exhibit high precision and have smooth internal and external surfaces.
Pulp Molding Trimming Molds
After drying, the wet pulp may undergo deformation, with certain areas experiencing severe deformation. When there is a high requirement for the external shape of the product or when significant precision is needed, the product needs to undergo a trimming process using trimming molds. These molds also require heating elements but do not have mesh molds. The products that require trimming should retain a moisture content of 25-30% during the drying process to facilitate trimming.
In practical production, it is challenging to control the moisture content, making it difficult for the products to meet quality requirements. To address this issue, some manufacturers have designed spray trimming molds, which feature spray holes corresponding to the areas that require trimming. During operation, the thoroughly dried product is placed into the trimming mold, and simultaneously, the spray holes on the mold spray water and apply heat and pressure to the product, achieving the desired trimming effect.
Conclusion
The above are some mainstream pulp molding molds and manufacturing processes currently in use. AGICO produces and sells various models of pulp molding machinery, and can provide various types of molds assorted. Please feel free to contact us for more information!