AGICO Seedling Tray Machine
AGICO has over 20 years of research and production experience in the field of pulp molding equipment. It is a professional and reliable manufacturer of seedling tray machines that can provide you with complete pulp seedling tray solutions. Our paper seedling tray machine is an rotary pulp molding machine that combines efficiency, sustainability, and versatility. Designed to meet the demands of modern agriculture and horticulture, this machine produces high-quality seedling trays and a wide range of other pulp-molded products by simply changing molds (such as egg trays, fruit trays, shoe trays, etc.), offering unmatched flexibility for diverse market needs.
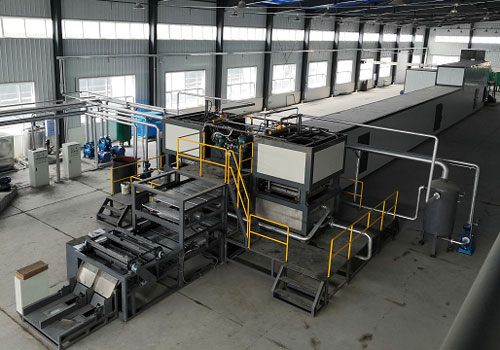
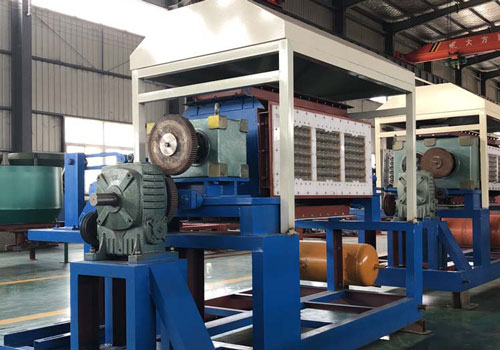
Contact us now for more machine details!
Advanced Technology for Superior Products
The nursery tray making machine employs vacuum molding and hot pressing technology to deliver pulp-molded products with exceptional precision and structural strength. These trays feature excellent durability and breathability, providing an optimal environment for healthy plant growth. Its rotary design offers three drum types—single-panel, four-panel, and eight-panel—to cater to varying production scales. Each panel can accommodate three or four mold sets, resulting in six different machine models. These models support production capacities ranging from 1,000 pcs/h to 8,000 pcs/h, making them suitable for businesses of all sizes.
Integrated Solution for Optimized Workflow
Our seedling tray machine is more than just a high-performance production unit; it is part of a complete production solution. Paired with pulping equipment, drying systems, and packing machines, it forms an integrated production line that streamlines the entire process, boosting efficiency and reducing operational costs.
Eco-Friendly Innovation for a Sustainable Future
This machine represents a significant step forward in sustainable manufacturing. By using renewable pulp as the primary raw material, it minimizes reliance on plastic products, aligning perfectly with global sustainability goals. Each seedling tray reflects our commitment to green agriculture, enabling customers to achieve their business objectives while contributing to environmental protection.
Customizable to Meet Diverse Needs
Our nursery tray machine is designed to adapt to your specific production requirements. With various models and mold configurations available, it can accommodate everything from small-scale pilot production to large-scale industrial manufacturing. We are dedicated to delivering tailored solutions that help our customers stand out in a competitive market.
Contact us today to learn more about our Seedling Tray Machine! Request a product brochure or schedule a demonstration to discover how our solution can drive your production efficiency and environmental impact.
Seedling Tray Production Line Specifications
Model | ZMDTF3-1 | ZMDTF4-1 | ZMDT3-4 | BTF-4-4 | ZMDT3-8 | ZMDT-4-8 | ZMDT-5-8 | |
Production capacity(pieces/h) | 1000 | 1500 | 2000 | 2500 | 3000 | 4000 | 5000 | |
Forming mould quantity | 3 | 4 | 12 | 16 | 32 | 40 | 60 | |
Total power (kW) | 34 | 41.2 | 53.7 | 57 | 90 | 150 | 153 | |
Electricity consumption (kW/h) (70% of the total power) | 23.8 | 28.84 | 37.59 | 39.9 | 63 | 105 | 107.1 | |
Labor force | 3-5 | 4-6 | 4-6 | 4-6 | 5-7 | 5-7 | 5-7 | |
Materials consumption (kg/h) | Paper | 85 | 102 | 170 | 212 | 298 | 425 | 459 |
Water | 255 | 306 | 510 | 636 | 894 | 1275 | 1377 | |
Fuel consumption | Coal | 50 | 60 | 83 | 104 | 125 | 208 | 208 |
Natural gas | 22-32 | 26-36 | 37-47 | 46-56 | 56-66 | 92-103 | 92-103 | |
Diesel | 18-28 | 22-32 | 30-40 | 38-48 | 46-56 | 77-87 | 77-87 |
*Please note that the schemes in this chart are not absolute and can be customized. We will design unique equipment solutions for each customer to ensure the best production efficiency for them.
Need a quotation? Contact us now!
Why Paper Seedling Tray?
Seedling transplantation is a crucial method for achieving high yields and efficiency in modern agriculture. Common seedling containers include pulp seedling trays, plastic seedling trays, and ceramic seedling pots. Among these, plastic trays have poor breathability, leading to longer recovery periods for seedlings. Additionally, plastic products are non-biodegradable, challenging to recycle, and contribute significantly to environmental pollution. In some regions, farmers use manual soil potting for seedlings, which is labor-intensive and time-consuming. Moreover, variations in soil texture, such as sandy or clay-heavy soils, make this method difficult to implement on a large scale.
In contrast, pulp seedling cups offer an affordable and high-quality solution. They provide excellent breathability, promote optimal seedling growth, and are naturally biodegradable, making them environmentally friendly. As a result, pulp seedling cups have become the preferred choice for many growers, with vast market potential.
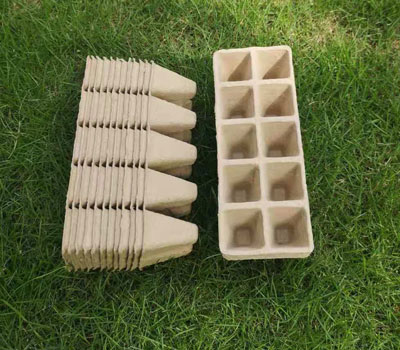
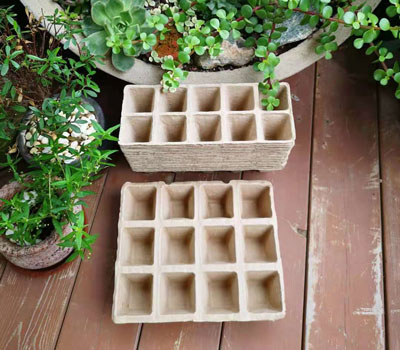
Advantages of Pulp Seedling Trays
Wide Range of Raw Materials: The trays are made from materials such as waste paper, cardboard, wood pulp, bamboo pulp, sugarcane bagasse pulp, and other plant fibers. These materials are abundant, easily accessible, cost-effective, and enable the recycling and reuse of biomass waste.
Simple and Efficient Production Process: The manufacturing process includes pulping, vacuum molding, drying, and shaping. It is straightforward and involves short production cycles, enabling large-scale, rapid, and automated production.
Eco-Friendly and Labor-Saving: The inherent properties of pulp seedling cups allow them to support water-based seedling cultivation. During the later stages of plant growth, the cups naturally degrade without harming the environment. This eliminates the need for manual collection, offering an eco-friendly, time-saving, and labor-efficient solution.
Compact and Lightweight Design: Pulp seedling trays are smaller and lighter than expanded plastic containers. They can be stacked for easy transportation and storage, reducing logistical costs.
Get in touch now to start your seedling tray production!
Core Technology of Seed Tray Machine
AGICO’s pulp seedling tray production equipment adopts the dry pressing pulp molding process. This traditional production method separates pulp molding, drying, shaping, and trimming into distinct stages. The process begins by forming wet pulp molds on the molding machine, which are then transferred to an external drying unit for drying (external drying method). Finally, the products undergo shaping and trimming to complete the production process.
Compared to the wet pressing process, the dry pressing method produces pulp-molded products with slightly less surface smoothness. However, it features a simpler production flow and relatively lower energy consumption, making it a more cost-effective option for manufacturing seedling trays, where surface appearance is not a primary concern.
Paper Seedling Tray Production Process
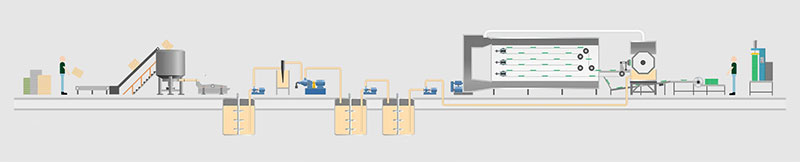
The production process consists of the following steps:
Step 1: Measure pulp raw materials according to the required ratio, and use a hydrapulper to process the pulp, achieving a slurry concentration of 3.5%–4.0%.
Step 2: Pass the processed slurry through a dual-function refiner, where it undergoes cutting, fibrillation, and refining to obtain uniform pulp.
Step 3: Mix the refined pulp with white water, and add chemical agents such as waterproofing agents, wet strength agents, and dry strength agents. Stir the mixture evenly to prepare the blended pulp.
Step 4: Transport the blended pulp through pipelines to the molding machine. Use vacuum filtration to dewater the pulp and form wet seedling tray blanks.
Step 5: Spray the wet seedling tray blanks: At a temperature of 40–50°C, add silica nanoparticles to a polymethyl methacrylate-ethyl acrylate polymer solution, stir for 10–20 minutes, and then mix in an ethanol solution. Spray this mixture evenly on the surface of the wet seedling tray blanks.
Step 6: Dehydrate the sprayed seedling tray blanks, hot press them for shaping, and perform trimming to produce fully biodegradable, fluorine-free pulp-molded seedling tray products.